Introduction to Solar Panel Production Equipment
The production of solar panels is a complex and multi-stage process that involves various types of equipment designed to enhance efficiency and ensure quality. At its core, solar panel production commences with the processing of raw materials, primarily silicon, which is harvested from quartz. One of the essential machines in this stage is the crystal growth furnace. This apparatus is responsible for converting raw silicon into high-purity ingots, which are subsequently sliced into thin wafers. These wafers serve as the foundational element of solar cells.
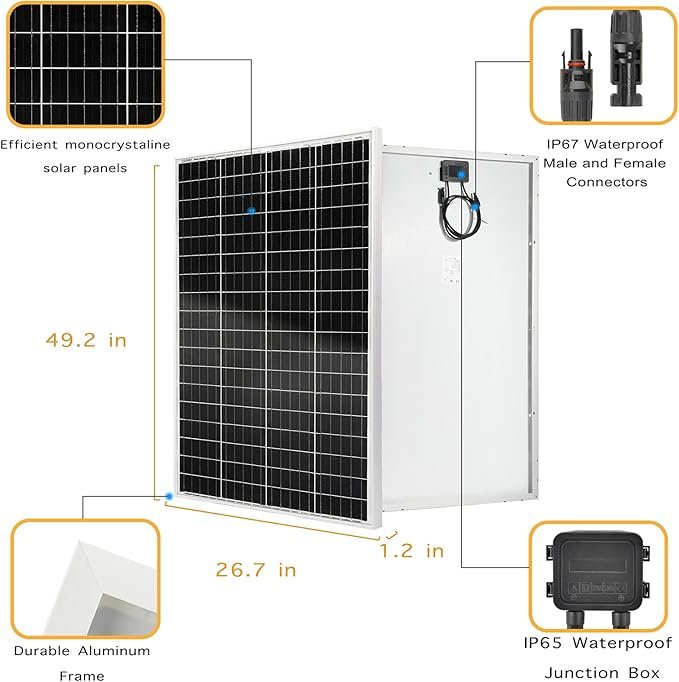
Following wafer fabrication, the next crucial equipment is the photolithography machine, which utilizes sophisticated processes to deposit conductive materials onto the wafer surface, creating the necessary photovoltaic cells. The precision and reliability of this equipment are vital, as any inaccuracies can lead to significant inefficiencies in power generation.
Once the photovoltaic cells are created, they undergo a process known as doping, which involves adding impurities to enhance electrical conductivity. The diffusion furnace plays a key role in this stage by facilitating the introduction of dopants at controlled temperatures, ensuring optimal functionality of the solar cells.
Subsequent to the doping process, another significant piece of equipment is the laminator. This machine is responsible for encapsulating the solar cells within protective materials, safeguarding them against environmental factors. The laminating process is critical for ensuring durability and longevity, factors that are paramount for the overall performance of solar panels.
Finally, once the panels are assembled, they are subjected to thorough quality inspections using automated testing equipment. This ensures that each solar panel meets the strict performance standards required for effective energy generation. In essence, each type of equipment used in the solar panel production process contributes significantly to the efficiency, quality, and reliability of the final product, highlighting the importance of investment in advanced manufacturing technologies.
Key Materials Used in Solar Panel Manufacturing
Solar panel manufacturing relies on a variety of materials, each contributing uniquely to the efficiency and longevity of the panels. A primary component in this process is silicon, which serves as the main semiconductor in photovoltaic cells. There are two prevalent forms of silicon used: crystalline and thin-film silicon. Crystalline silicon is known for its high efficiency and durability, while thin-film silicon can be produced at a lower cost but offers reduced efficiency. The sourcing of silicon is critical, as it requires high purity for optimal solar energy conversion.
Glass is another essential material in solar panel production, primarily used for the protective front layer of the panels. The glass must possess specific qualities such as low iron content to enhance light transmittance and durability to withstand environmental factors. Typically, tempered glass is utilized, benefiting from increased strength and resistance to impacts and harsh weather conditions. The transparency of the glass directly influences energy absorption, hence its significance in fabricating quality solar panels.
Metals, particularly silver and aluminum, are important for conducting electricity in solar panels. Silver is commonly used for the conductive paste in photovoltaic cells due to its excellent conductivity, although it is one of the costlier components. Aluminum, on the other hand, is utilized in the panel’s frame and back sheet, offering a lightweight yet robust structure that enhances the overall durability of the solar panel.
Lastly, encapsulants are vital in the production of solar panels, as they bond the layers together and provide protection against moisture, UV rays, and mechanical damage. Ethylene-vinyl acetate (EVA) is typically used for this purpose, ensuring that the cells remain intact and operational over their lifespan. The choice and quality of these materials are crucial for maximizing the efficiency and reliability of solar panels in harnessing solar energy.
Functions of Each Part in Solar Panel Construction
Solar panels are intricate assemblies designed to convert sunlight into electricity efficiently. Each component plays a crucial role in ensuring optimal performance, longevity, and reliability. The primary building block of a solar panel is the solar cell, which is typically made of silicon. Solar cells are responsible for the photovoltaic effect, where sunlight excites electrons, creating an electric current. These cells are arranged in a specific pattern to maximize exposure to sunlight, whereby each cell’s efficiency is imperative for the overall energy output of the panel.
Backing materials serve as the foundation for solar cells, providing mechanical support while offering electrical insulation. These materials, often made from polymers or composites, are important for protecting the solar cells from environmental factors and ensuring the panel’s durability. Moreover, the backing aids in thermal control, helping to maintain optimal operating temperatures which can directly affect performance.
Protective layers are essential for safeguarding the solar cells from physical damage, dust, and moisture, all of which can impede functionality. These layers are usually composed of glass or transparent plastic, enabling sunlight to penetrate while reflecting heat away. The quality of the protective layer can significantly influence the lifetime of the panels, as it must withstand the rigors of various environmental conditions, including hail, rain, and UV radiation.
Finally, the framing of a solar panel provides structural integrity. Typically made from aluminum, the frame allows for easy installation and enhances stability during high winds or extreme weather conditions. This component not only supports the solar panel but also facilitates heat dissipation, further optimizing the energy generation process. The interconnectivity of these parts is vital; their individual roles converge to create an efficient energy-generating system capable of withstanding time’s wear and tear.
Innovations and Future Trends in Solar Panel Production
The solar panel industry has witnessed substantial advancements in recent years, particularly in manufacturing technologies and materials. Innovations such as bifacial solar panels—designed to capture sunlight from both sides—have significantly enhanced energy efficiency. These panels utilize high-transmission materials, which allow them to harness reflected sunlight, thereby increasing overall productivity. The integration of advanced coatings also results in better light absorption, translating to improved electrical output.
Moreover, the evolution of solar panel production is being propelled by the introduction of perovskite solar cells. These cells promise to deliver high efficiency at a lower cost compared to traditional silicon-based panels. Perovskites also simplify the manufacturing process, making it more accessible and reducing the environmental impact associated with production. The potential for scaling up perovskite-based technology remains a focal point for future research, aiming to further optimize performance and longevity.
As the industry pivots towards sustainability, there is a growing emphasis on recycling materials used in solar panel production. Efforts to develop cost-effective recycling techniques are underway, enabling the recovery of valuable components such as silicon and metals from decommissioned panels. This presents an opportunity not only to mitigate waste but also to significantly reduce the carbon footprint associated with extracting and processing raw materials. Additionally, manufacturers are investing in cleaner production technologies, focusing on minimizing emissions and resource consumption throughout the entire lifecycle of solar panels.
In conclusion, the solar panel production sector is on the brink of transformative changes driven by innovative materials and sustainable practices. By prioritizing advancements in production efficiency and environmental responsibility, the industry is poised to meet the growing energy demands while contributing to a greener planet.